Case Study:
Physical Security LLC.
THE CLIENT
Physical Security LLC.
THE SERVICE
Track & Trace
Table of Contents
Executive Summary
Challenges
CodeREADr Solution
Results
POI Quote
Executive Summary
Physical Security LLC, is a contract glazing company operating from the Birmingham, Alabama metropolitan area. They fabricate, assemble, and glaze curtain wall for installation in high-rise, healthcare, commercial, and institutional buildings. For example, you can see their glass exteriors from the Sears Tower, NCIS Headquarters, Raleigh-Durham Airport, and the Pentagon. Despite being considered a small business, PS’ manufacturing facility spans 120,000 square feet with millions of dollars in product.
Challenges
As this operation grew, PS sought a solution to track their assemblies with details. For example, they wanted to track the silicone manufacturer. Also they had to track the serialized batch of silicone for every assembly of a building. Moreover, each unit had to record this data during an assembly in case there is an issue post-assembly.
Thus, Jason Bush, an IT Manager at PS, requested a service, where each unit can have information attached at each point in the production process. The units would have a unique QR code when first arriving on the assembly line. Then, you would tag the assets with their manufacturing information. For example, they would have project number, glass manufacturer & details, silicon manufacturer & details, and unit ID. Then, this info follows and timestamps each unit from the assembly, shipping, storage, and ending with the installation.
The greater benefit would come from a programmatic solution to easily store, share, and edit this data to different levels of the production process through installation. Also, Jason showed the challenge of needing to be able to save unique historical data for the QR codes.
CodeREADr Solution
Thus, CodeREADr created Table Builder. This curated service allows the client to build parent tables with child table views. Also, it enables authorized app-users to scan a barcode and answer data-collection prompts as fields within defined tables.
For the company’s needs, this enables its tracking process to include all relevant data attached to a unique QR code. Also, the Table Builder service validates against a master database of assets tagged with QR stickers. First, when an asset is at the assembly line, the PS CodeREADr system scans it. Secondly, it and prompts the user to input the first set of information key to the company’s warranty process.
Thirdly, the QR code builds upon an attached record of data. Fourthly, you can add or edit it. Fifthly, it will tag the resulting info to the code and store it neatly in a table. Then, you can access it from an online web view and download it as a file for review.
Also, yes/no questions and short answer entry fields prompt the users along the way to share with Jason’s team everything they may need to create a robust log for warranty use. As the assets move from their manufacturing facility to installation, users can access relevant info in the process. For some, answers from prior steps are both visible and editable while for others, they can only view the data relating to the prior steps
in production before adding their own quality assurance pieces.
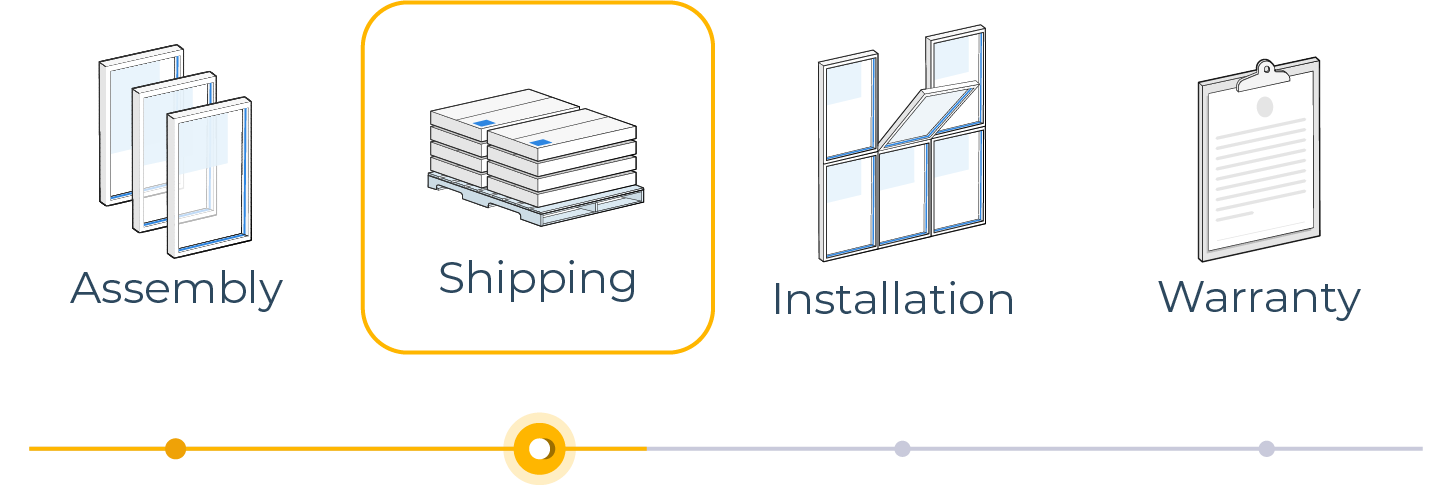
Results
After delivering our new Table Builder service to Jason, PS greatly reduced the time spent in administrative processes. Prior to implementing CodeREADr services, you had to document every unit and the information with hard copies or electronic spreadsheets. After assembly, you need to record the related warranty information that is specific to each unit.
“This real-time entry of warranty and quality control information using only the mobile phones our employees keep in their pocket accomplished Physical Security’s main goal for CodeREADr,” noted Jason. “The ability to access the data from a custom web portal and the rapid entry is huge from an IT perspective. I am not having to maintain scanners, and the related data storage nor do I have to worry about user intervention.” On the job site, we can utilize this same information for even greater utility. Also, users on the job site scan the assembled units before installing them on the building facade. This records a highly accurate timestamp of the physical installation for each unit. Also, project management can pull reports giving detailed information of exact and real-time job progress.
Jason and all of PS have been overwhelmingly satisfied with the CodeREADr’s solution.
POI Quote
“Being in IT for nearly 25 years, I have dealt with many software vendors and support teams. These guys have the support and diligence to rival any large vendor and are to be commended. On first contact, CodeREADr welcomed us to an extended trial of their product. I tested their product and sample apps and quickly noticed the potential to give us what we were looking to achieve.”
“I was unaware of the abilities and capabilities of QR codes. In the beginning, it was obvious I was wanting a little more out of their product than currently implemented. There were quite a few discussions of what we were looking to achieve, our current processes, and how the final product should appear to my users. They took on the task and provided a usable product in a timely manner as well as supporting us with ‘tweaks’ to our code as needed. In the end, CodeREADr was able to customize a very slick and easy to use solution that has more than accomplished our initial goals.”